Research and development projects
Active-nano
- performs research and development projects;
- carries out pilot projects on estimation of the planetary mill capabilities;
- develops technologies of the high-energy milling and production of composite powders;
- supplies prototype-scale lots of powders and performs technology transfer.
To meet Customer requirements we carry out research on the optimal process conditions. These conditions are determined first of all by the material properties. For the Customer material treatment to be effective, it is necessary to optimize such process parameters as:
- time of milling;
- acceleration;
- material of the grinding bodies;
- size of the grinding bodies;
- mass ratio of the grinding bodies and the milled material;
- medium of milling.
To estimate the capacities of the high-energy density milling equipment we use planetary mills MPP-1 and Gefest-3.
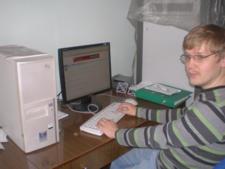 |
Search for the literature data along with an expert work with scientific papers and patents help to find our way in the ocean of scientific and engineering information. Dr. Alexander A. Vanin is analyzing information on the technical solutions available in the world literature.
|
The technical task is formulated in discussions with a Customer. For instance, it is necessary to obtain a composite powder with ceramic particles uniformly distributed in the metallic matrix. Requirements concerning particle size and purity are discussed. The composite powder obtained will consequently be compacted and sintered. The work purpose is therefore to improve the mechanical properties and heat resistance of the dispersion-strengthened alloy.
Search for the literature and patent data is undertaken by using all possibilities of the modern databases available in the Internet.
Task execution: ceramic powder and metal powder are milled and activated in a planetary mill. The following treatment stage is milling of the ceramic and metal powders together (mechanical alloying) to obtain the necessary composite material.
At each stage of the technology development we monitor such powder parameters as:
In some cases, when it is necessary to investigate the material behaviour on heating, thermal analysis is used.
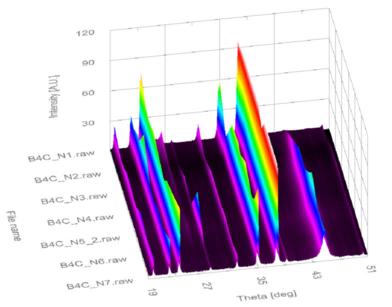 |
3D chart of the X-ray data dependence on the time of mechanical treatment.
|
If necessary, milling can be performed in an inert gas (argon) atmosphere.
A Customer receives the powder samples and a scientific technical report containing characteristics of the original and milled powders. Powder characteristics are determined using a number of methods of physico-chemical analysis. Evaluation of the throughput rate of large planetary mills for the particular process studied is undertaken.
A pilot project usually represents the first attempt of the treatment of a new material in a planetary mill and a test of productivity of the milling equipment. While selecting the milling conditions we take advantage of our experience accumulated during our work with planetary mills. The result of a project is represented by thoroughly characterized powders, namely, an original raw powder sample and 4-5 samples of the powders obtained at different milling conditions. Basing on the samples characteristics, it is possible to monitor milling process: for instance, whether particle size is decreasing, or agglomeration is taking place; whether “saturation” is reached (i.e. further milling does not cause any changes in particle size).
The Customers run their own tests and inform us which of the specimens has the best performance properties. After such a feedback it is possible to produce the powder in necessary quantities at the conditions chosen.
The development of the technology on a larger scale is much more demanding and requires checking the impact of various engineering parameters. We are ready to supply prototype-scale lots of powders. Technology transfer is also possible.
We readily collaborate in the field of the development and production of new materials including nanomaterials. Partners in R&D programs are welcome!
|