Frequently asked questions
Question: What is the minimal particle size that can be obtained during milling in the planetary mills used? Answer: The minimal particle size depends first of all on the material treated. Routine milling in planetary mills allows us to obtain submicron powders of the average particle size equal to several hundreds nanometers. Quite often, customers want to obtain a powder having the average particle size less than 100 nm. In such a case, it’s necessary to specify whether the nano-powder itself (for example with the particle size of 20-30 nm) is required to solve the engineering problem. The issue is that it is rather difficult to deal with the nano-powder. Thus, nanoparticles rise in the air on opening the vessel, they readily agglomerate, and some problems also arise during their compaction and sintering. In practice, it is more convenient to use the mechanically activated powder that can be referred to as nano-structured. In such a powder, the size of particles can reach several hundreds nanometers but the particles consist of grains (crystallites) having size less than 100 nm. Such a powder can be easily sintered. One can find some examples of milling of silicates and tungsten carbide on the “Materials” page. We succeeded to obtain the average particle size (calculated according to the BET method data) of 95-100 nm for WC and 50-60 nm for layered silicates.
Question: Is it possible just to mill a material without performing any measurements? Answer: It is meaningless since it implies to take one “black box”, make some manipulations with it, and obtain another “black box”. In such a case one doesn’t know what happened to a material: whether the comminution has taken place or, vice versa, the particles are growing (as it happens sometimes), whether oxidation, chemical reaction, phase transition, agglomeration have occurred, or any contamination has appeared. Can it be helpful to a customer?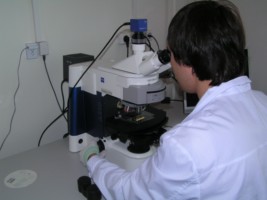 We prefer not to act blindfold but to understand what processes are taking place during the mechanical treatment. We consider that it is absolutely necessary to perform initial and final control, monitor all characteristics (particles size and structure, phase composition, impurity content) for the initial and treated powders, and afterwards, to provide to the customer a series of samples obtained in different conditions of milling. It is possible to decide what sample has the best (optimal) characteristics. After that we can obtain necessary quantities of the material at the milling conditions chosen..
Question: What rotation rates of the jars are used? Answer: According to the manufacturer’s data, the planetary carrier rotation speed of 422 rpm and the jars rotation speed (around their own axes) of 800 rpm are used in the laboratory planetary mill MPP-1. Nevertheless it is not correct to compare different planetary mills only according to the planetary carrier rotation speed. There is one more parameter, the distance from the rotation axis to the jar center (the radius of the movement of the jar center), that matters. It is for the point of the jar center that the acceleration value is calculated. For the MPP-1 mill, the acceleration is 28 G. The centrifugal or normal acceleration appears when a point moves round a circle. The normal acceleration vector always points to the circle center while the absolute value is calculated in the following way:
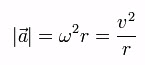
|