Milling of minerals
The present investigation was devoted to the milling and characterization of a layered silicate. The initial powder contained particles having size up to 100 µm and was milled in a planetary mill MPP-1.
Equipment and investigation methods
In accordance with the performance specification the comparative studies of the initial sample and the sample treated in the MPP-1 planetary mill were performed using the following experimental methods: To determine the powders’ specific surface area the gas chromatographic method with argon thermodesorption (BET) was used. The determination of phase composition and crystallite size of the powders was carried out by the X-ray phase and X-ray structure analysis using the diffractometer DRON-4 M (СuKα radiation, Ni filter, Johansson monochromator), equipped with the interface RS 232; the program ANALIZER developed particularly for the finely dispersed materials was used. Microphotographs of the samples were made using the transmission electron microscope Tesla BS 613C.
Initial data
The sample contains about 40 % wt. % SiO2, along with oxides of magnesium, iron, aluminium, calcium, nickel, chromium, and other elements.
Results
BET method
Results of the layered silicate particle specific surface area measurement by the BET method are represented below in the Table 1.
Table 1. Particle specific surface and average size calculated according to the BET method. Measurement accuracy is 5%.
Milling time, min
|
Specific surface area, м2/g
|
Particle average size (BET), nm |
0 |
26 26,3 |
88 |
2 |
36 37 |
63 |
4 |
38 40 |
59 |
8 |
50 51 |
46 |
14 |
53 |
44 |
Particle average size calculated according to the BET method data is 44-60 nm for milled powders. Average values of the powders’ specific surface area grow with time of milling up to 40-50 m2/g.
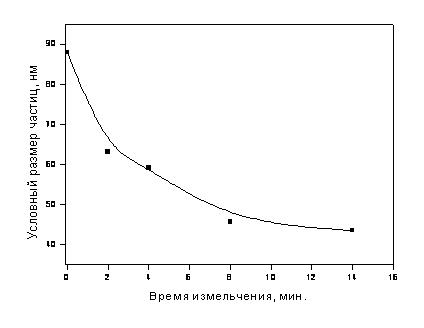 Dependence of the average particle size (according to the BET method data) upon time of milling in the MPP-1 planetary mill.
X-ray structural analysis
The crystallite size for the milled silicate samples is in the range from 50 to 100 nm:
Milling time, min.
|
Crystallite size, nm |
2 |
103 |
4 |
49 |
The samples investigation by the transmission electron microscopy method allows one to specify the powders’ microstructure. There are comparatively large fragmented and fibrous particles (having size of several microns) in the initial sample. The sample also contains some submicron particles. After the treatment in a planetary mill for 4 minutes, the comminution of long fibers occurs and the content of sub-micron particles (fiber fragments having width about 20-40 nm) increases significantly. Besides, the amorphous phase is formed. The maximal degree of the particle size reduction was attained for the sample milled for 14 minutes.
|
Microphotograph of the initial layered silicate sample. The enlarged photo can bee seen here.
|
|
Microphotograph of the layered silicate sample milled in a planetary mill for 14 min. This enlarged photo can be seen here.
|
Conclusions
The powders having the specific surface area in the range from 40 to 50 m2/g, the average crystallite size of 50 nm (as estimated by the X-ray structural analysis), and the average particle size about 50-60 nm (as calculated using the BET method) were obtained by milling of the initial sample in the planetary mill MPP-1 for 4-14 minutes. These powders were partially aggregated. However, the particle aggregation degree was successfully lowered by the ultrasonic treatment of the aqueous powder suspension. The minimal particle size corresponding to the cross-sectional size of the separate fiber fragments is about 20 nm according to the electron microscopy data.
|